Windmills of Scoraig
An informal tour, by Hugh Piggott year 2000
This tour is always out of date :-)
things change too fast
CountZ.com
since 7th October
2000
Back to Hugh's
homepage
This is an very brief guide to the windmills which provide electricity
to households on a small peninsula with no road access or power lines (called
Scoraig). I hope I don't step on too many toes by telling it like
it is and describing our experiences of various commercial makes, old and
new.
Links to machines below:- Ampair, AIR,
LMW,
Proven,
Survivor,
winco,
chinese
My own designs, including also the
African
AWP3.6
and the ITDG alternator
Here is some text to read, while you wait for the pictures to load
Intro Hugh Piggott
Windpower fanatic. Born Scotland 1952, educated
Edinburgh and Cambridge. After graduation, went back to the land
in NW Scotland where I remain. For 4-5 years I did without electricity
except what I could rob off 12V vehicle systems on rare shopping expeditions,
by connecting an elderly car battery to bits of loose wire. This
ran my cassette tape machine.
In 1978 I got seriously bitten by windpower and have been
partly or totally obsessed with it ever since. This is a windy place
and very dark in winter, so there is a strong sense of victory when you
can harvest energy from a crashing gale and swamp the house in dazzling
light. Lots of bits would drop off my windmill(s) but I persevered
and ended up making windmills for most of my neighbours. They still
ring me up when they need the windmill fixed. There are about 30
windpower systems within a few minutes' walk of my house.
In the late 1980s I decided to broaden my perspective
and I started working on windmills built by others. I was amazed
to find that bits drop off them too (I thought it was just me). In
fact it turned out that I was pretty good at fixing windmills by then and
so I did some work with manufacturers, testing and developing machines,
in the demanding conditions we have here. I also wrote up some of
my ideas and helped teaching courses at the Centre
for Alternative Technology in Wales. Stopped milking a
cow and bought a fax machine.
More recently I have designed a windmill for manufacture
in Africa
and also installed some direct AC hydro systems. I find hydro
very exciting because it provides much more energy at lower cost (on a
good site) and you do not need batteries. I hate batteries.
In 1999 and 2000 I have worked as consultant to a TV company,
designing and installing a wind/hydro system for castaways
on an island.. I have also been doing another developing world project
for ITDG, culminating in a permanent
magnet alternator design you can download for free.
Ancient History
When I moved here in 1974, most people used oil lamps for lighting,
because this was simpler than running a diesel generator. There is
not a lot of money around on Scoraig, but the atmosphere is generally quite
relaxed. Planning and discussion are favorite occupations.
The working day is often curtailed by bad weather, so there is no point
in being in a hurry.
One neighbour had an old battery charging 'Freelite' made by Lucas.
I would take my tape machine 12 volt battery along to him for charging,
but I also messed around trying to build a windmill myself. The first
attempt was a bicycle-hub dynamo which I sat on the rooftop. It worked,
but it was really noisy in the house. In those days I was a 'back
to the land' hippie type, and my resources were pretty thin.
.
.
I struggled for a long time to build something workable, but that's
another story. We had a lot of fun finding out what worked and what
didn't. This single bladed machine for example (built by my cousin,
Topher
Dawson) worked after a fashion but the pitch control system never quite
got perfected.
I had a lot of help from friends like Alan
Bush, Alan Beavitt, and countless others, and I read some books.
Around 1980, I made quite a number of 2-bladed windmills based on 24volt
dynamos from Austin Champ Jeeps. Many of them are still in use today,
although they have been repaired and modified a few times over the 20 years..
Output is around 300 watts from a 6 foot diameter rotor.
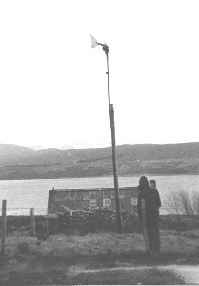
and as the trees have grown, I have had to increase the heights of
them.
Here is an old Winco being moved to
a new site by a tractor, complete with its tower. Sadly this machine
is no longer working today. The linkages wore out and the commutator
gave constant problems.
Year 2k
During the 1990s a number of windmills were imported to Scoraig,
and I learned a lot more about the art of wind turbine mechanics. Much
of what I have done has been repair work, because I was using secondhand
parts, or fixing up something which fell apart unexpectedly. I developed
some designs of my own at the same time, and
published
some stuff about how to build small wind turbines.
What follows is a guide to the ones which are around in year 2000 (I
am struggling to update it in places too), and what stuff has happened
getting to here. Awful things do happen to small wind turbines,
as you will see, but remember - these machines are working, and bringing
joy and light to their owners. Being a mechanic I mainly see the
breakdowns.
Links to machines below:- Ampair, AIR,
LMW,
Proven,
Survivor,
winco,
chinese
My own designs, including also the
African
AWP3.6
and the ITDG alternator
Here is the LMW3600 which was installed
here, to heat the Primary school, in 1990.
the
view is southeast, up the loch.
This machine taught me that I was not the only person who had problems
producing a good design of windmill. We had a lot of problems with
the LMW during the first few years.
It makes a very loud humming noise which swells and reverberates.
The tail furling system didn't work properly, and it ran too fast,
which wore out the blade edges.
This in turn caused vibration, fatigue and failure of vital parts such
as the tail, and the alternator mounts.
In other words it fell apart, repeatedly.
I have modified the tail so that it furls at about 2kW and it has now
gone for several years without problems. We have gradually grown
used to the noise and we don't notice it these days.
some blade erosion in this picture.
Ultimately, this has been a successful installation, and it keeps the
school supplied with ample electricity, although it never could have provided
sufficient heat. The average output is under 1kW - not enough to
heat a building of that size. But the rotor diameter is large (5m.
16') and so it catches plenty of power in low winds, to keep the school
supplied with light, and power for computers, vacuum cleaner, photocopier,
etc.. And in windy weather it does produce enough surplus to heat
one room to a very nice temperature.
Not many small windmills are built to give good service in very windy
conditions.
They work OK on other sites, where there is less wind, but in an exposed
coastal location like ours the problems show up early.
Some of my neighbours have owned AIR
machines from Southwest Windpower (Arizona), but their life expectancy
has been about 2 weeks. Commonest failures are burned out electronics
and broken blades.
After-sales service has been absolutely brilliant. Spare parts
and replacement machines have been supplied promptly and without quibbles.
On one site the machine was upgraded to an 'industrial' (very expensive)
version free of charge, and this has lasted almost for a whole year on
one occasion.
Here is a picture of the site.
The owners live in the little house on the right. We had to fix
a piece of sheet metal to the tail after the yaw bearing started to seize
up. It's quite a powerful machine for its size, given a good wind.
But we all know about it when it is running - it's almost as noisy as the
LMW in normal conditions, and when it hits full power it's louder than
a chainsaw.
The other family who had an AIR machine were lucky enough to be given
an old Marlec FM1800 as a replacement. This is a sturdy machine,even
though the electrics are horribly complicated.
We have now moved this machine up the hill to get away from the trees.
We tried Marlec Rutland72 watt machines for a few years, but
the stators would normally fail after about one year, and you can only
replace the stator a few times before the bearings work loose, and then
you need a new alternator. Marlec gave up making spare stators for
their older models, and I began to lose interest in Marlec.
Especially since they 'upgraded' the fm1800 by giving it only 2 blades.
One machine which gets full marks is the Ampair
Hawk
.
It only produces 100 watts but at least it goes on doing it through
outrageous storms, and years of service with little or no attention.
The only thing which has been a real problem is the regulator. These
tend to burn out. Brushes can also give problems but this is rare/unknown
on Scoraig.
For 2 years I ran a Survivor S3000
wind turbine, which I had bought ex-demonstration. It was rather
out of date, and is now badged 'Synergy' instead. I believe they
have also put sliprings on it. I never had problems with cable twist,
but I did have problems with rain running into the yaw bearings, so that
they fell apart and the machine flew off the tower top. I also had
a blade root failure (see picture) where the mounting plate cracked across.
It ran for a few hours with 2 blades. This type of cracking has happened
to me before, with a Whisper 1000 'spring plate'. Seems like a highly stressed
piece of plate.
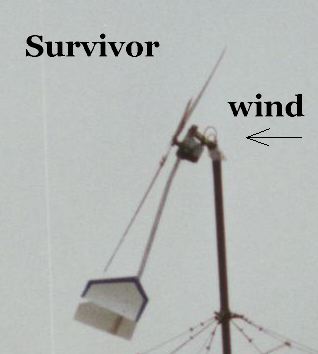
The furling system is fascinating, based on a hinge at the topmost point,
from which the windmill hangs. High winds blow it upwards until the
tail and blades are horizontal.
Another 'downwind' machine, which has fared much better here is the Proven.
Here is the 2.5kW machine at Scoraig. I did some development
work with it around 1995, leading to the use of double springs in the governing
system. This windmill does not furl by turning away from the wind
as most others do. It governs its blade speed accurately using centrifugal
force to alter the pitch of the blades.
The system puts quite a high stress onto the blades and springs, which
have sometimes cracked, and failed. For example the blades on the
Castaway machine at Taransay have just failed after very nearly two years
of high wind duty. One blade disappeared entirely.
Cracks in the polypropylene blades occur at the hinge points.
Proven have recently introduced Polyurethane
hinges for their blade roots and these are proving to be much more
robust.
Scoraig is also the home of the prototype Proven 6kW machine which
is owned by my cousin Topher Dawson (boatbuilder and wind turbine blade
fabricator).
No more machines were built in this 'monocoque' style. The beam
on the right is for a balance weight, which is also unique to this prototype.
This windmill has worked well for about 3 years, with some nursing from
its owner. Unfortunately, the production versions still have some
problems to be worked through, but as usual, Proven
Engineering are working on solutions!
In this picture you can see the magnet rotor inside the alternator.
The cover was removed to improve cooling, and it looks nice too, wheeling
along.
Here's a picture of a chinese wind turbine
which I have been testing. As supplied there were problems with its
balance and its furling system. After some early problems in 1998,
it has settled down to be quite a nice reliable machine .
PS we did have a blade fly off during the winter 2000-2001 and I have
now put the blades from the survivor on it.
this is typical of the sort of 'swift and grotty' repairs which keep scoraig
windmills going on a shoe-string long after they would have been abandoned
on other sites.
We also have some machines of my
own design here, for example the brakedrum windmill
(as written up in the Plans available from Picoturbine.com)
and the African 36
(see
this link too)
This wind turbine powers our home.
and now another one power Scoraig Secondary School
And one for william at Rhireavach..
another is located at Badrallach on the tarmac road, 10 miles from Dundonnell:-
Here is another one on Scoraig, installed sumer of 2000 for Bill Burstall
In this one you can see 3 AWP machines out of the 7 which are now up
and running in this area.
We have had some early problems related to manufacturing quality of
the alternator shaft, and cracks in the fibreglass blades, but there are
no real technical challenges remaining for this machine. It works.
It just remains to get on and install them.
Another one to shout about is the 4kW heating machine I built with
help from Alan Bush and African Windpower in Zimbabwe (who made the stator
for me). African Windpower are working on a production version.
The blades were made
on Scoraig by Topher
Dawson.
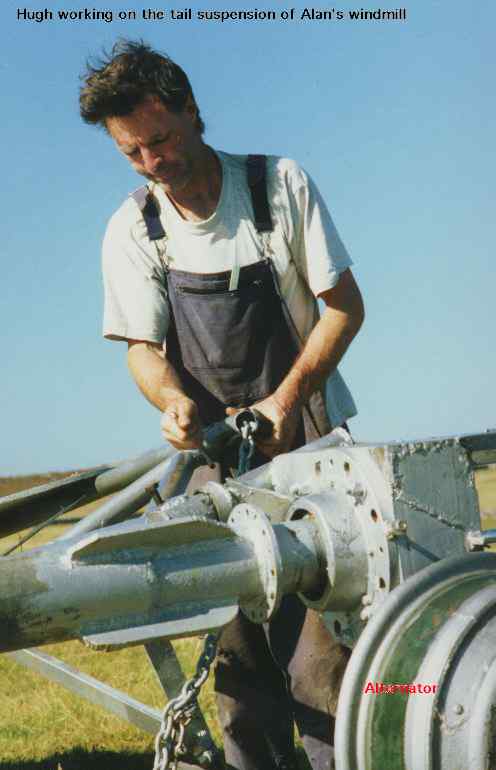
In the next picture you can see it being lowered for repair in June
2000.
It does have occasional problems, with rotor balance, stator insulation,
and suchlike, but it has run pretty consistently for nearly three years.
Here are a couple of pictures of locally produced
prototypes using the alternator I have designed for ITDG for local
manufacture in sri lanka
and peru. see also this link
for details of the alternator and how to build one.
Back to Hugh's
homepage