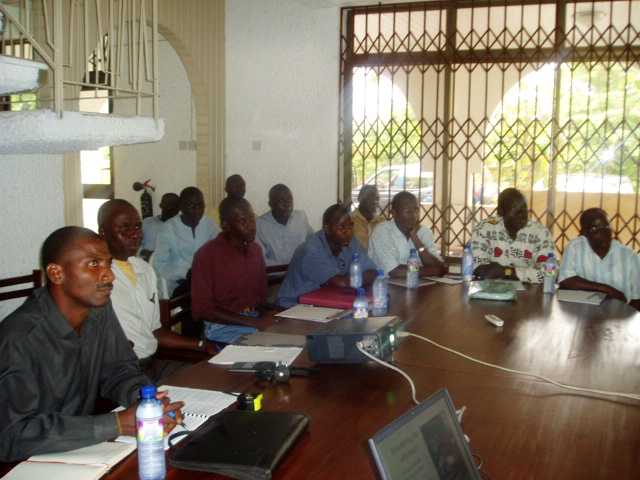
On Monday morning we started the course at EnterpriseWorks
offices, getting to know each other.
I showed some video footage and Powerpoint presentations
to introduce the basic design ideas.
Then we moved to Accra Polytechnic where we spent most
of the course using their ample workshop facilities.
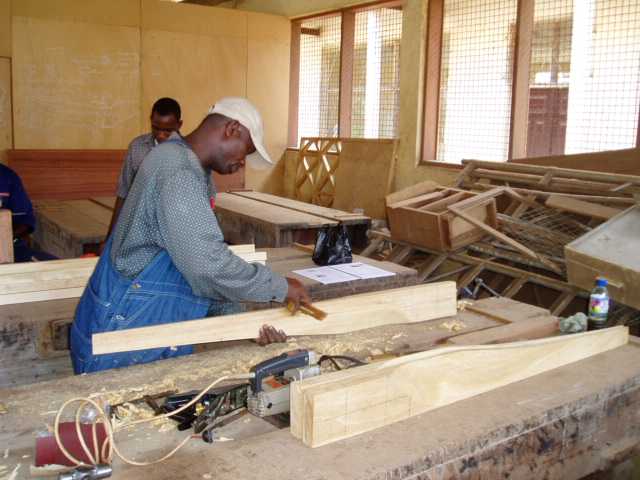
MacCourage Alorvor of Mighty Sparks Company Ltd carving
blades from local wood.
Courage found us some very nice wood called 'emory'(?).
This is a smooth hardwood with interlocked grain.
It was nice to work with when unseasoned but we did find
out that it warped later.
In the future it will be necessary to season the wood
first.
Michael Atidigah of MICKYLOG CRAFT was also on the blade
carving team. I did find it hard to spend enough time with these
guys because their workshop was located a short walk away from the rest
of the action. At one point we discovered that Michael had used the
wrong table for the blade trailing edge drop. It's so easy to use
the thickness measurements by mistake. But this produced a blade
with very coarse pitch that would not work at all well. It's worth
being wary of this pitfall.
Checking the blade assembly to make sure that a stuff
will pass through it squarely. It definitely helps to drill an over-sized
hole in the part beyond the back disk. The stud fitted nicely.
Working with Andrew K. Etwire of Power World Ltd (holding
book) on the controller for the windmill.
Andrew has a lot of nice ideas. For example we
used a multi-meter to display battery voltage on the push of a button.
This gives low-cost, accurate readings without exhausting
the battery in the meter.
Moses Kattah winding coils assisted by Eric Siaw from
Seli Technologies.
Moses taught me that it is not necessary to set the reel
of wire up on an axle.
He takes it off the side of the reel. I would have expected
it to cause twisting and kinking but in fact it works fine.
Moses strips the enamel off the wire in the same way I
do - with a knife.
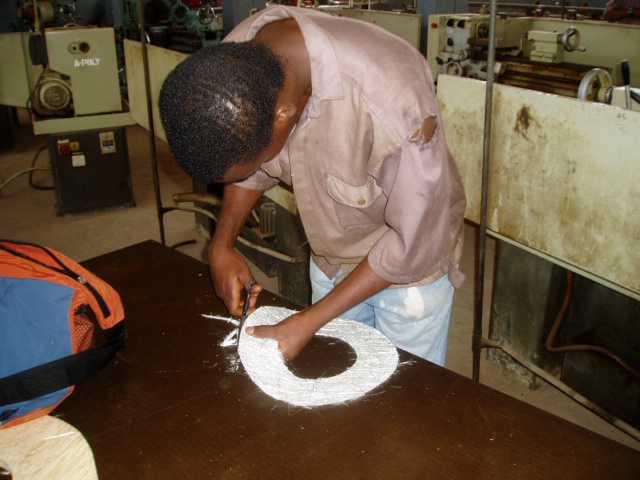
Cutting out the chopped strand mat and mixing the polyester
resin.
We used very heavy fibreglass, but that seemed to work
OK.
More of a problem was getting the right amount of catalyst.
I re-learned the hard way that you have to use a lot
less catalyst in high ambient temperatures.
It didn't seem that hot to me, but we had to use about
half of the catalyst
specified in the course manual (windmill plans) and we
also had to apply the silicone later to prevent it setting.
If things set too soon then you can't make a thin enough
casting.
The resin fumes were not too bad - in fact I don't think
I could smell them at all.
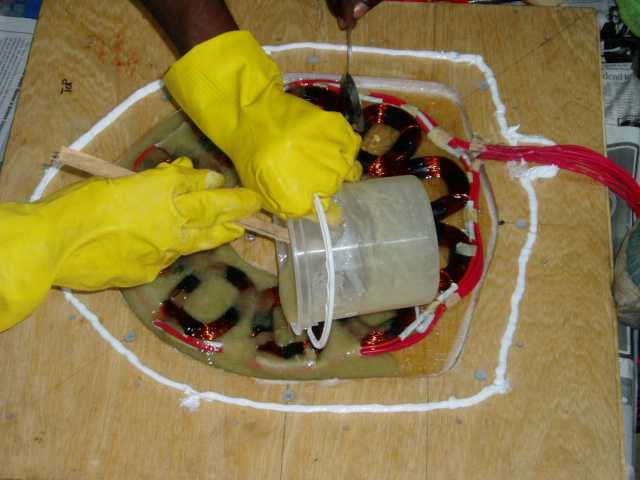
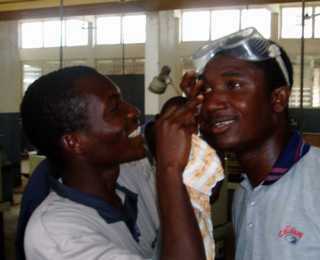
We used 'superglue' to fit the magnets to the disks.
This prevents the possibility of them moving in the moulds
after the lid goes on (as has happened a couple of times recently).
When the magnets snap down, the glue can spray out.
Eric Dor from Seli helps Boniface Taylor to get it out
of his eye. Eye protection pays off in the end.
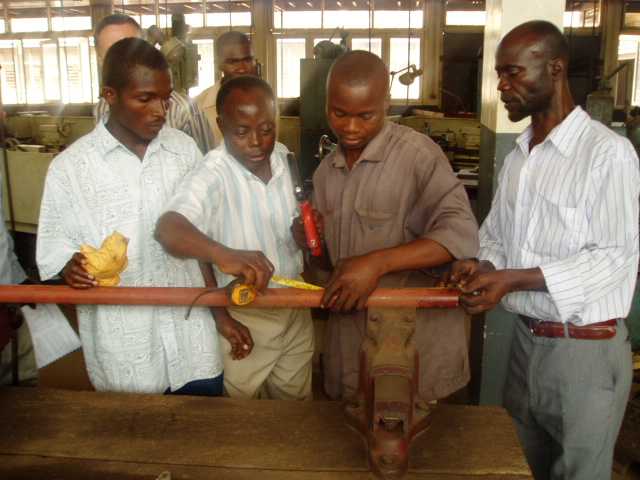
We used hacksaws for cutting. Much of it was done
by Sammy Nelson of Accra Poly (second from right in first picture)
but we also had the use a power saw that did a lot of
the heavy cross-cut work.
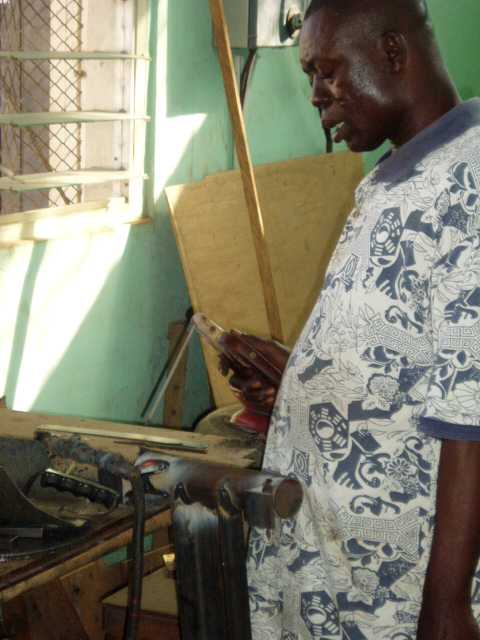
Frank A. Pobi of CSIR
did pretty much all of the welding, and we had no complaints.
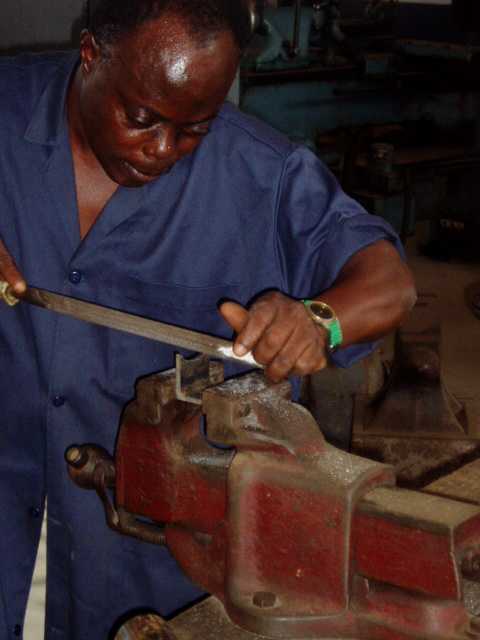
Joseph Dzansi of CSIR shaping the stator brackets.
We used 1" thick spacers to support the alternator
bracket above the table and fitted the stator lugs in contact with the
table.
In theory Ghana is metric, but it's just like the UK:
in practice most people talk in inches.
Sammy, Ken and Martin clamp the car axle in the correct
position prior to drilling the fixing holes.
The heatsink (supplied by Andrew) in its bracket (designed
by Frank.)
Emmanuel Ocansey of Money Technologies and Investments
(Centre) admires the tail hinge
which he personally cut out from 10 mm plate with a hacksaw.
Emmanuel gets my vote as the most useful person in the
workshop. He even brought a cordless drill.
Matt Kuach-Baiden of Solar Winds Engineering Services
playing with the partially assembled alternator.
It's fun to watch pieces of steel swarf walking around
the stator as you turn the back magnet rotor.
Mr. Baiden fits the front rotor. Note the jacking
screws in position. We had some problems with stud alignment, due
to paint on the rotor faces.
Joseph fits the blade assembly.
Here you can see the detail of the rectifier housing.
An insert on the left shows the rectifier with cover off.
Andrew had the idea of using a domestic twin socket-outlet
box. Very cost-effective, but it needs a lot of silicone to make
it waterproof.
Also note the small section of pipe welded onto the top
of the yaw bearing as a cable guide for the wires down the tower.
Wrap the wires over the guide, and tie them on with wire
ties.
Emmanuael tries the tail vane for size. A map of
Africa.
Maps have been in fashion since the 2003
workshop on Guemes island!
Frank with the tower-base. We made a tilt-up tower
using thick-walled 2" pipe.
Steel is very expensive in Ghana and it may be better
to use the local wood, suitably treated.